Feasibility Studies
CDI can carry out the feasibility study of the conveyor system in a comprehensive manner, from route selection, conveyor design to cost estimation.
Route Selection
The three-dimensional modeling of the route topography enables CDI to optimize civil works and the placement of elevated or ground-level steel support structures. Path optimization allows for comparison of design options to reduce cut and fill activities, eliminate material transfer points by proper placement of horizontal and vertical curves, and reduce potential conflicts with environmentally or politically sensitive neighbors. All this in turn reduces the final cost of capital (CAPEX) and the operating cost (OPEX) of the conveyor system.
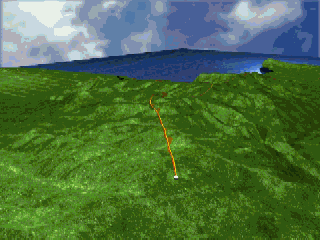
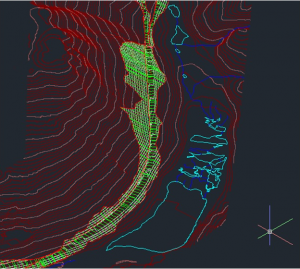
Conveyor Design
Depending on the project, regulatory and environmental requirements, CDI will meticulously engineer the selected types of conveyors, be it Standard Belt, Tubular Belt or other special conveyor, using our internal Beltstat software for static analysis of the conveyor and Beltflex to dynamic analysis. The conveyor design process specifies the power and location of the motors, the type of belt and idlers. It also includes the engineering of the conveyor components, such as pulleys, support structures and maintenance trolleys.
Capital cost estimate
CDI generally develops the capital cost estimate of the transportation system in accordance with the requirements of the AACEI (American Association of International Cost Engineers) estimation methodology to achieve the agreed precision range. The capital cost estimate includes the direct cost, such as the cost of mechanical components, structural cost, civil cost, etc. Indirect cost includes engineering, labor, freight, contingency, etc. Typically, the owner’s cost, such as permits and land acquisition, is independent, but can also be included.
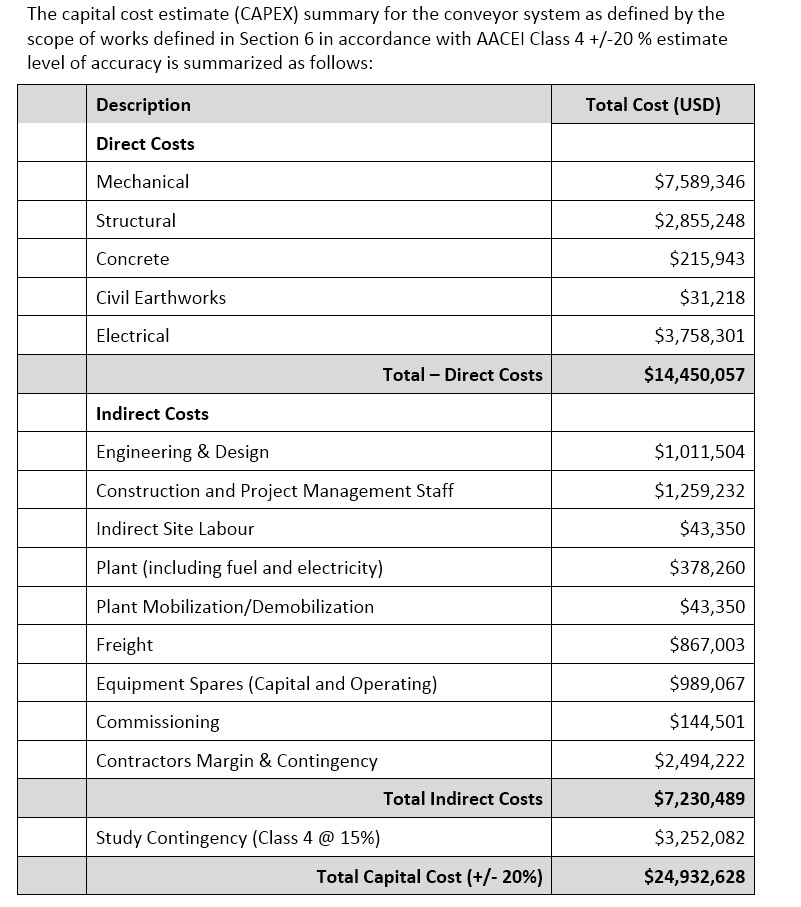
Estimate of operating costs
Operating expense (OPEX) is developed according to the AACEI methodology on the basis of an owner operator. The OPEX cost analysis includes:
- Power consumption
- Planning and supervision
- Cleaning and maintenance
- Inspections and lubrication
- Planned equipment maintenance and repairs
- Unplanned equipment maintenance and repairs
Maintenance costs are derived from:
- OEM maintenance practices and programming
- Equipment prices for main components
- Knowledge and experience in the industry
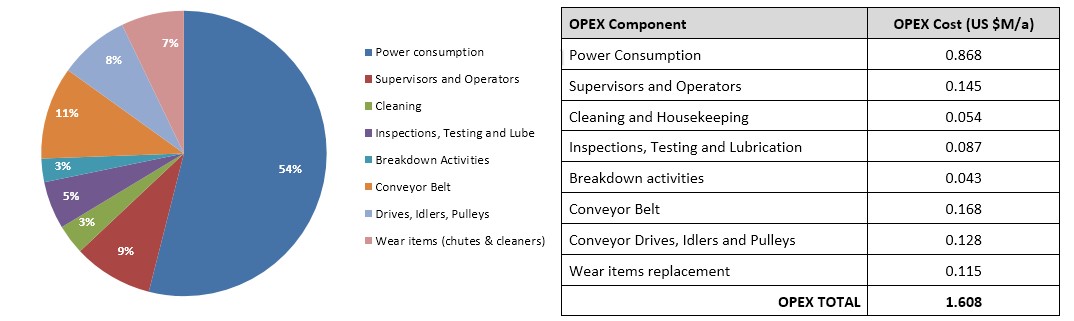
CDI can also go a step further by combining CAPEX and OPEX to optimize the life cycle cost of a given project. Multiple routing options and conveyor design options are included in this analysis to compare total life cycle cost with Net Present Value. The end result provides the end user with a much clearer financial picture so that better decisions can be made during the project planning stage.
